Hydraulique, électrique ou hybride, faites votre choix
La traditionnelle opposition hydraulique-électrique en termes de transmission de puissance est factice : les deux modes sont complémentaires et coexisteront pendant encore de longues années. La densité de puissance de l’un n’a d’égal que la facilité et la propreté de l’autre. Tout dépend des besoins des industriels. Le mode hybride (actionneur hydraulique et contrôleur électronique) tente de les réconcilier.
Depuis plusieurs années, transmissions hydraulique et électrique cohabitent dans l’univers de la machine-outil. Les avantages de la transmission hydraulique consistent essentiellement en une force de transmission élevée. La transmission hydraulique peut transmettre une force importante avec peu de perte de puissance, ce qui est idéal pour les applications de coupe et de formage. La durabilité est aussi meilleure : les composants hydrauliques sont généralement plus robustes et durables que les composants électriques, et donc mieux adaptés aux applications lourdes et intensives. Enfin leur faible coût d'exploitation par rapport aux systèmes électriques leur confère un avantage compétitif de taille. Mais a contrario, les systèmes hydrauliques nécessitent une maintenance plus complexe que les systèmes électriques, du fait des vérifications et remplacements réguliers des huiles et des filtres. À cet égard, ils présentent un risque de fuite d'huile. Ils sont aussi plus encombrants que les systèmes électriques, ce qui peut poser des problèmes d'espace dans les ateliers. Pour autant, les transmissions hydrauliques utilisées dans le secteur de la machine-outil cohabitent depuis plusieurs années avec les technologies électriques et hybrides. Leur image de marque ternie à l’origine par des problèmes de fuites entrainant une certaine réticence de la part d’utilisateurs soucieux de privilégier la propreté dans leurs usines et dans leurs procédés de production. Les moteurs électriques peuvent être facilement commandés pour atteindre des vitesses et des couples précis, ce qui permet d'obtenir une précision élevée dans les processus de fabrication. Les machines-outils électriques peuvent être facilement modifiées pour s'adapter à différents types de tâches en changeant simplement les outils et les programmes de commande. Enfin, l’apparition de la variation de vitesse a rendu les moteurs électriques plus efficaces, ce qui permet de réduire les coûts d'exploitation. Pour cet ensemble de raisons, les utilisateurs se sont délestés petit à petit de tout leur savoir-faire en matière d’hydraulique. Considérée comme plus propre, plus facile à installer et à piloter avec précision, la technologie électrique a su s’imposer comme le choix prioritaire, tant chez les fabricants que chez les utilisateurs de machines-outils.
Hydraulique versus électrique
Philippe Granchamp, responsable commercial pour les solutions d’automation chez Parker Hannifin, souligne en outre le risque associé à l’hydraulique : « cette technologie nécessite un environnement spécifique, compte-tenu du risque de fuite : formation des intervenants, permis feu requis… » Il confirme la recherche d’efficacité par les industriels : « nos solutions sont orientées vers le meilleur rendement possible. L’électrique gagne du terrain, mais l’hydraulique, de par sa densité de puissance, a encore de belles années devant lui. Nous proposons par exemple des solutions totalement électriques pour des efforts jusqu’à 12 tonnes sur une presse. » Le responsable commercial évoque également les solutions hybrides : un actionneur hydraulique contrôlé par l’électronique, avec une couche logicielle supplémentaire pour la remontée de données. D’une manière générale, électronique et hydraulique font bon ménage de longue date : « la synchronisation de vérins hydrauliques s’opère par un contrôleur électronique, comme avec le PACHC, pour Parker Automation Controller Hydraulic Control). » Efficience, rendement, connectivité sont devenus les maîtres-mots de l’industrie actuelle. De ce point de vue, l’électrique l’emporte haut la main : « Le rendement d’une solution pneumatique est de l’ordre de 20 à 25 %. En revanche, son coût est très bas. L’hydraulique atteint un rendement de près de 60 %, mais l’hydraulique a besoin d’un moteur et d’une pompe électrohydraulique pour générer pression et débit. Le rendement atteint 80 % avec l’électrique ! » « Les utilisateurs nous demandent également des solutions compactes. Le mètre carré coûte cher. » L’avantage d’une solution hybride (vérin hydraulique contrôlé par l’électronique) est la possibilité d’y adjoindre un variateur de vitesse pour moduler la vitesse de déplacement du vérin. « Cela nécessite bien sûr un groupe électrohydraulique piloté par variateur pour générer une pression et un débit spécifique au vérin » précise Philippe Granchamp. Les programmes qui pilotent ces solutions sont ouvertes : « nous proposons une base Codesys qui offre une grande facilité de programmation aux automaticiens » indique le responsable commercial. Le module PACHC est associé au contrôleur PAC120 (master/slave). En termes de connectivité, il est compatible avec la plupart des standards : OPC UA, Profinet IRT/IO, Ethernet IP, Modbus TCP (master) Canopen. Sa capacité tolère jusqu’à 40 axes (deux par module). L’autre solution proposée par Parker Hannifin est une gamme de moteurs, avec couple refroidissement air / eau TMW /TMA/TKW/TKA. Il fournit des transmissions à fort couple en première monte et en rétrofit, avec pour caractéristiques : une connectivité et une maintenance prédictive, une réduction des encombrements, un rendement élevé. Il est destiné aux marchés spécifiques de l’extrusion, de l’injection, les malaxeurs et autres machines spéciales.
Centrales connectées
Bosch Rexroth est bien sûr présent avec ses transmissions hydrauliques. Dans ce cadre, parmi les gammes proposées, sa pompe à cylindre fixe, entraînée par un moteur asynchrone. Un accumulateur peut compléter l’équipage et permettre de réduire la taille de la pompe. Le fabricant précise : « Le gros avantage, c’est le prix et la mise en œuvre rapide. La transmission full hydraulique existe également avec une pompe à débit variable équipée d’une régulation hydraulique P/Q/Pw ou électronique, ce qui donne de la dynamique à la transmission et permet d’optimiser la puissance installée par un contrôle du ratio P/Q (pompe SYDFE, HS5 …). » Bosch Rexroth propose également des centrales classiques pour la machine-outil comme les ABSKG et ABPAC pour les plus grosses machines.
Des solutions plus innovantes ont fait leur apparition, comme les transmissions hydrides, les centrales connectées et les axes autonomes. Des centrales compactes et de nouvelle génération sont arrivées sur le marché, avec la Cytropac et la Cytrobox. Compactes, économes en énergie, connectées, ces centrales sont particulièrement adaptées à la machine-outil. La technologie Sytronix de Rexroth (vitesse d’entraînement variable) ouvre de nombreuses possibilités dans le contrôle et la dynamique des transmissions notamment avec les solutions SvP 5020 et 7020. Enfin, concernant les mouvements linéaires qui pourraient être nécessaires dans une machine, les solutions Cytromotion et CytroForce, axes autonomes électrohydrauliques, sont un vrai plus. En effet, elles ne nécessitent plus de centrales hydrauliques car ces dernières sont intégrées dans le vérin qui embarque la génération hydraulique et le contrôle, et cela de manière très compacte. À noter que Bosch Rexroth offre la commande de la machine en complément de la transmission, qu’elle soit hydraulique, électrique ou hybride. Sa gamme d’automatismes et de composants d’interface homme/machine « ctrlX » permet le contrôle des axes.
Moteurs haut rendement
Stöber propose principalement ses moteurs électriques, pneumatiques et hydrauliques en fonction des applications et des besoins. « Nous faisons appel aux moteurs électriques à haut rendement pour des axes " intelligents " de positionnement, synchronisation, gestion d’effort, régulation de vitesse, en raison de son très bon rendement énergétique. Pour cette raison, il devrait continuer à être le moteur principal dans le futur. Nous sommes d’ailleurs régulièrement consultés depuis quelques années pour remplacer des moteurs hydrauliques au rendement médiocre qui nécessite une installation encombrante et un entretien régulier » souligne Erwan Chevanse, responsable commercial. Dans cet ordre d’idées, Stöber procède au remplacement régulier de moteurs hydrauliques par des moteurs servo électriques brushless. Le fabricant a développé un programme spécifique pour ces applications de presse électrique avec une gestion du couple du moteur combinée à la maîtrise de la vitesse selon différentes positions, qui donne des axes plus flexibles et plus simples à gérer pour les utilisateurs, et ce sans entretien. Erwan Chevanse ajoute : « Avec l’augmentation des coûts de l’énergie, la recherche du système le plus efficace va être l’une des clés pour la vente des futures machines. Le moteur électrique apparaît donc comme le plus adapté au monde de demain. Mais il a aujourd’hui quelques limites : son coût, comparé à celui du pneumatique pour les tâches simples et répétitives, et son manque de puissance comparé à l’hydraulique pour les tâches lourdes de forte capacité. »
Nidec Leroy-Somer propose pour sa part une large gamme de moteurs et de variateurs adaptés au marché de la machine-outil. Parmi les solutions, citons la gamme Dyneo+ de moteurs synchro-réluctants assistés d’aimants permanents à haut rendement IE5. Ces moteurs offrent un coût total de possession (TCO) faible, avec un retour sur investissement (ROI) court et une maintenance réduite. Dyneo+ inclut plusieurs services digitaux grâce à la nouvelle application interactive Systemiz. En vitesse variable intégrée, la solution Commander ID300 a été optimisée pour le pilotage des moteurs asynchrones IMfinity de Nidec Leroy-Somer : peu énergivore, alliant haute performance et fiabilité, ce système décentralisé excelle dans la machine-outil.
Un soufflet inspiré par la nature
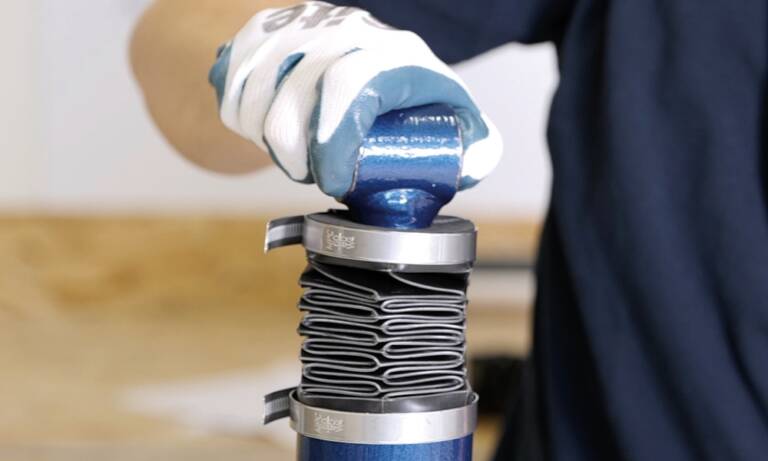
Eclore est une start-up française basée à Nantes et fondée en 2019 par Pierre-Gauthier Le Boulch, ingénieur Mines de formation. Avec son équipe de quatre personnes, il a développé un soufflet de protection pour les vérins présents dans les machines-outils. Particularité de ce soufflet : son pliage façon origami est inspiré notamment par le ver à tabac : « Pierre-Gauthier a travaillé pour l’industrie spatiale. Dans ce cadre, il a réfléchi à la fabrication de voiles solaires pour les satellites. La contrainte était alors d’obtenir l’encombrement minimal pour ces voiles pliées » détaille Mathieu Cazard, responsable commercial d’Eclore.
La nature propose des solutions optimales, c’est pourquoi la technologie que développe Eclore prend exemple sur elle. Le pli est l’une de ces optimisations. Formé sous la contrainte, il s’adapte aux sollicitations mécaniques. Dans la nature, on retrouve le pli à toutes les échelles : formations géologiques, végétaux, animaux. Ainsi, le ver de tabac est un exemple très représentatif du pli avec une forme corporelle singulière.
Le soufflet est en polymère. Sa composition plus précise appartient au secret industriel. Mais le composant a subi les tests avec succès, et totalise 10 millions d’utilisations sous contrainte, avec des pressions de 0 à 6 bars. Le kit proposé comprend le soufflet, un adaptateur et un collier de serrage.
Eclore travaille par ailleurs à un nouveau vérin. Pierre-Gauthier Le Boulch entend lever un million d‘euros pour ce projet, et ambitionne de passer à 25 salariés en 2023. À suivre de très près, donc.
Maximisant la productivité et la qualité des produits grâce à un contrôle précis des automatismes, le variateur Unidrive M optimise les performances tout en offrant fiabilité, flexibilité, universalité et réduction significative du coût global de l’installation et de l’exploitation. Pour des applications à haute dynamique, le variateur Digitax HD, en complément, offre tous les avantages d'un système modulaire avec un bus DC commun pour un pilotage multiaxes et la flexibilité d’un variateur autonome. Ce variateur peut aussi piloter un moteur asynchrone ou synchrone à aimants en mode vectoriel boucle fermée ou boucle ouverte, grâce à un mode de contrôle adapté. Il est disponible en version communication Modbus RTU, en version Multiprotocoles (Ethernet / Profinet RT) et version Ethercat. Il reste possible d’intégrer les autres bus de communication : PROFIBUS, POWERLINK, DEVICENET, CANOPEN.
La variation de vitesse au cœur
KEB offre une palette de solutions dédiées aux machines-outils et aux machines spéciales. Au cœur des solutions proposées, les variateurs de vitesse : « Les variateurs F6 et S6 de KEB sont des composants bien établis dans la chaîne cinématique d'un large éventail d'applications. Néanmoins, ils font l'objet d'un développement continu, par exemple en ce qui concerne le logiciel », explique Tobias Grabbe, responsable du développement logiciel chez KEB. « Tout récemment, par exemple, nous avons mis en place une fonction de protection utile pour les résistances de freinage sous-jacentes pour notre COMBIVERT F6. Cette fonction élimine notamment la nécessité de manipuler et de régler les données relatives aux résistances de freinage. » La variante Pro des variateurs offre d'autres caractéristiques à l'entraînement adéquat : par exemple, en plus des diagnostics CAN et RS482/232, qui sont également intégrés dans les deux autres variantes d'appareils, la version dispose d'Ethernet comme interface de communication possible. Safety over EtherCAT (FSoE) met en œuvre le profil de sécurité des variateurs F6 et S6, et une interface multi-encodeurs est possible en option avec la variante PRO.
La gamme de puissance évolue de 0,75 kW à 450 kW et offre la capacité de contrôler une large variété de technologies de moteurs différentes. Ces variateurs de vitesse sont conçus pour être utilisés dans des domaines d'application très différents. Grâce à sa fonction de sécurité sans codeur, la version PRO en particulier convient aux machines à bois, entre autres applications.
Et l’hydraulique ?
L’un des clients d’Hydac, un fabricant international de machines-outils, a remarqué chez certains de ses clients des résidus de combustion dans l'huile, des éléments filtrants détruits, voire des pannes des composants électroniques installés dans le système hydraulique. L'objectif était d'éliminer les dysfonctionnements de l'électronique et de prolonger de manière notable la durée de vie de l'huile et des éléments filtrants. Les experts et l'équipe en charge des machines-outils chez Hydac ont analysé le problème sur le site de l'un des opérateurs de machines concernés. Après avoir réalisé des mesures, des analyses d'huile et des enquêtes à cet effet, il s'est vite avéré que l'opérateur utilisait des huiles hydrauliques de nouveau type avec une conductivité faible dans ses machines-outils, ce qui était à l'origine des problèmes. Hydac a réalisé d'autres analyses avec différentes combinaisons d'huile et d'éléments filtrant au FluidCare Center HYDAC. Ces essais ont débouché sur le développement de la technologie d'éléments filtrants Stat-X. La technologie a été testée avec succès auprès du client final et a pu réduire au minimum la charge électrostatique dans le système. Les décharges électrostatiques sont ainsi évitées. La solution a été entre-temps installée dans toutes les machines du fabricant.
Composants à la pointe
Mayr propose une large palette de composants pour la transmission de puissance dédiés aux machines-outils : limiteurs de couple, accouplements, freins de sécurité. Les limiteurs EAS-compact promettent une protection contre les surcharges dans une multitude de variantes disponibles, avec des couples de déclenchement allant de 0,65 à 1 500 Nm, une transmission du couple sans jeu, une exécution avec maintien de la charge pour les axes inclinés ou verticaux disponible sur demande, une limitation du couple fiable et une grande simplicité de réglage du couple par graduation. En termes d’accouplements, la solution ROBA-DS opère jusqu’à 20 000 tr/min, dans une plage de couple de 35 à 110 000 Nm, et propose un accouplement à paquet de lamelles sans jeu, d’une très grande rigidité torsionnelle, complètement équilibré à G 2.5 et à nuisances sonores minimales.
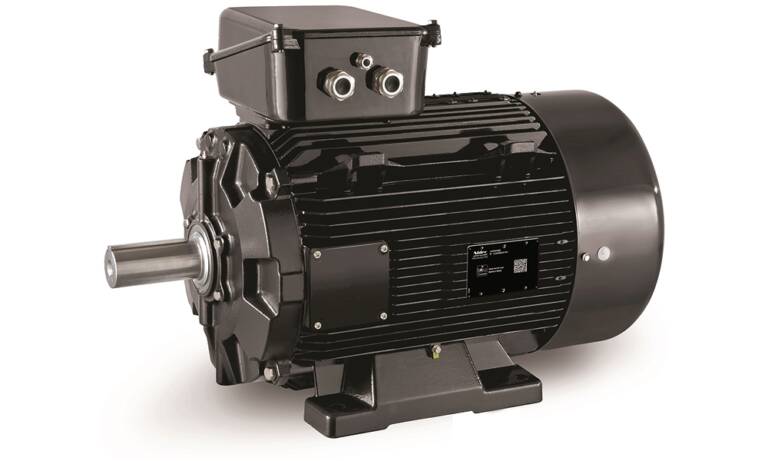
Mandrin de serrage
Siam Ringspann propose sa solution de serrage avec ses mandrins expansibles indirects à douille HDDS, dédié à l'usinage des pièces d'engrenages comme les roues dentées et les pignons droits ou coniques. Le fabricant explique : « Dans le domaine des mandrins de précision pour machines-outils, nos systèmes expansibles permettent le bridage à la position 0 et la transmission du couple pour les opérations de tournage, fraisage, rectification ou équilibrage des pièces de révolution. »
Concrètement, une pile de disques de serrage Ringspann est placée sur un boulon de traction. Une douille fendue, qui est vissée sur une bride, est placée sur le dessus du boulon de traction. Lorsque le mandrin de serrage de la douille actionné par un disque mécanique est activé, les disques de serrage s'étendent de manière exactement identique sur toute la circonférence, tout en ouvrant la douille fendue.
Rockwell Automation, la connectivité améliorée
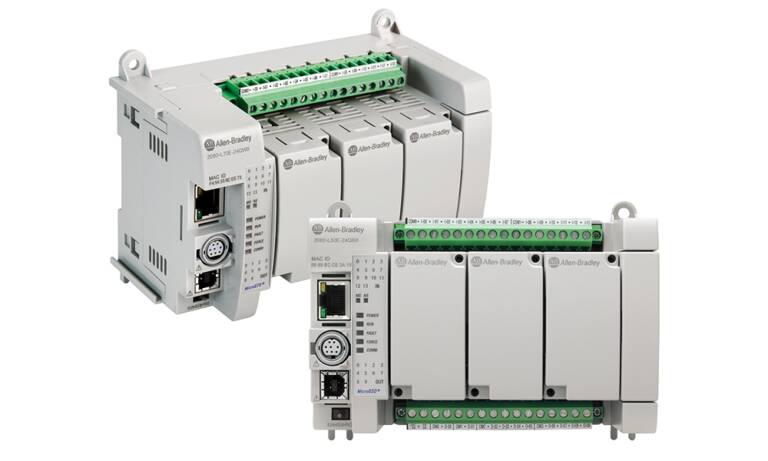
Les constructeurs de machines peuvent réduire les délais et les coûts d’ingénierie avec la nouvelle version des automates Allen-Bradley Micro850 et Micro870 2080-Lx0E, ainsi que la mise à jour du logiciel Connected Components Workbench de Rockwell Automation.
Les automates 2080-Lx0E proposent une meilleure connectivité et optimisent les opérations de conception grâce à la nouvelle fonction de messagerie implicite de classe 1 et acceptant jusqu’à huit périphériques EtherNet/IP. Ces modèles rationalisent l’intégration des automates aux variateurs par une prise en charge des variateurs PowerFlex Série 520 et Kinetix 5100 sur EtherNet/IP avec des points prédéfinis et des instructions de bloc fonctionnel définies par l’utilisateur (UDFB) préconfigurées. Mieux encore, l’environnement de conception familier et intuitif simplifie la programmation et la gestion des flux de travail.
La version 21 du logiciel Connected Components Workbench est le minimum requis pour assurer la prise en charge de la messagerie implicite de classe 1 par les automates Micro850 et Micro870 2080-Lx0E. Les améliorations apportées aux automates et au logiciel contribuent à améliorer la productivité des opérations industrielles tout en abaissant les coûts. Les utilisateurs bénéficient ainsi d’un système de commande simplifié et mieux connecté pour leurs conceptions automatisées.
L’ensemble permet également de réduire les tâches de programmation et les délais de dépannage, simplifiant le développement de machines autonomes réalisées avec le système de commande Micro de Rockwell Automation.
Au cours de ce processus, la douille fendue est raccourcie, principalement en raison de la géométrie conique de la bande de déformation, ce qui entraîne le retour du composant serré sur l'équipement. En ajoutant un manchon central, le mandrin de serrage de douille actionné par disque mécanique obtient la rigidité souhaitée. « Avec une précision inférieure à 5µm pour une tolérance jusqu'à IT10 du diamètre à brider, il permet de reprendre une pièce sur une portée ultra courte et n'a aucun risque de fuite, contrairement à un mandrin hydraulique standard » précise le fabricant. Il ajoute que le mandrin HDDS peut être considéré comme un système hybride permettant d'utiliser l'actionneur de la machine-outil, hydraulique ou électrique, et de le convertir en une force de serrage mécanique au niveau du mandrin.